Industrietrends 2024: Cloud-basierte Lösungen, erweiterte Sicherheit und Metaverse
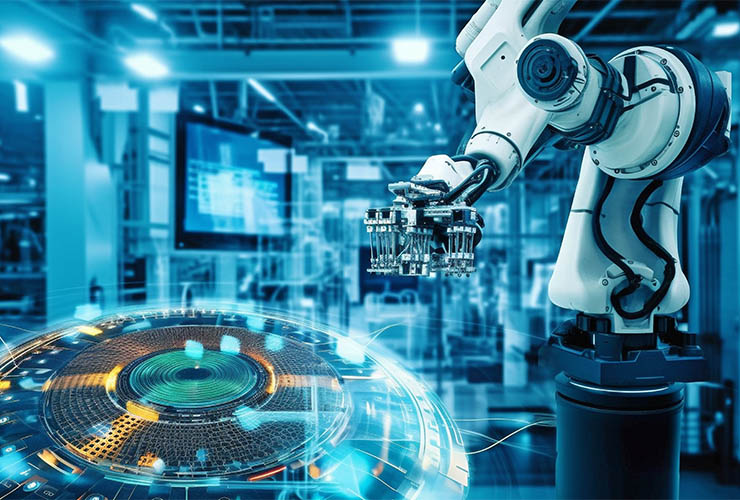
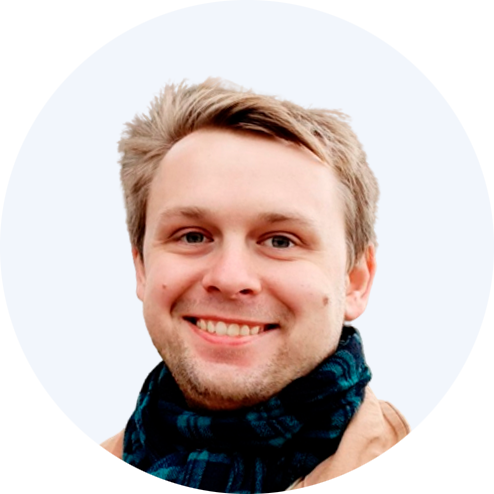
In welche industriellen Lösungen sollten Sie investieren und sie in Ihre langfristige Strategie einbeziehen? Da wir unsere Kunden weltweit mit der Entwicklung von fortschrittlichen Software- und Hardwarelösungen unterstützen, konnten wir nicht umhin, die neuesten Trends in der industriellen Automatisierung zu erkennen, die den Markt vorantreiben.
Sieben Treiber der Branche
1. IT/OT-Konvergenz: virtuelle SPS und IIoT-Integration
2. Konvergenz von Kommunikationstechnologien
3. Integration von Cloud und Analytik
4. Erhöhte Sicherheit: SIL 3 Software-Konformität
1. IT/OT-Konvergenz: virtuelle SPS und IIoT-Integration
Da die Industrie bestrebt ist, die Hardwarekosten für Produktionsanlagen zu optimieren, gibt es eine deutliche Verschiebung hin zur Konsolidierung der Serverinfrastruktur. Ergänzt durch Echtzeitserver werden lokale Server in Fabriken zum Hauptbestandteil industrieller Netzwerke.
Ein wichtiger Aspekt dieses Trends ist der Übergang aller Sensoren und Treiber zur Ethernet-Physical-Layer-Ebene (Protokolle wie Ethernet APL und Ethernet SPE). Die Controllerebene verschwindet und wird durch virtuelle SPS ersetzt, die Teil lokaler Server in Fabriken ist.
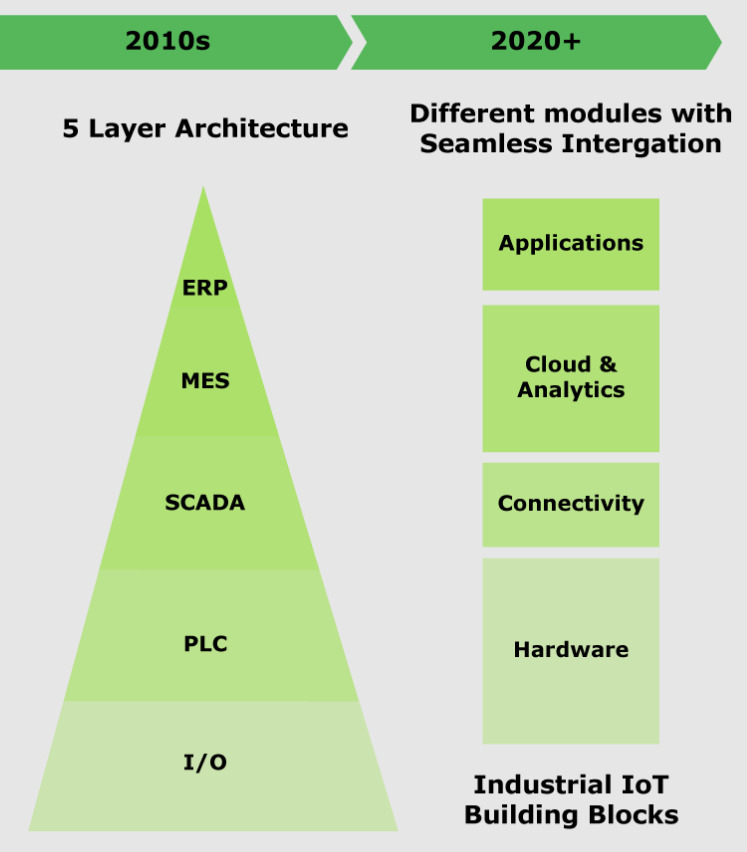
IT/OT-Konvergenz: Übergang von einer 5-Ebenen- zu einer 4-Ebenen-Architektur
Eine virtuelle SPS wird in einer virtuellen Umgebung mit Containern und Hypervisor-Technologien anstelle von Hardware betrieben. Um virtuelle SPS zu implementieren oder zu orchestrieren, können Benutzer einen beliebigen lokalen Server wählen.
Traditionelle elektrische Signalstandards wie 4-20 mA, 0-20 mA, 0-10 V und andere verschwinden vom Markt und machen Platz für effizientere Ethernet-basierte Kommunikationslösungen. PROFIBUS ersetzt weitgehend PROFINET, und Technologien wie IO-Link stehen kurz vor dem Übergang zu IO-Link Ethernet, allerdings mit einer stärkeren Neigung zu PROFINET.
Nach Ansicht der Codesys-Experten werden in der Industrie 5.0 OT und IT vollständig verschmolzen. Anstatt mehrere Controller zu kaufen und zu installieren, genügt es, die bestehende IT-Plattform im Netzwerk mit virtuellen Controllern zu bestücken und diese zentral zu verwalten.
2. Konvergenz von Kommunikationstechnologien
Die Entwicklung der Kommunikation in der industriellen Automatisierung folgt der Standardisierung, Interoperabilität und Integration von industriellem Ethernet und Echtzeitkommunikationsprotokollen. Dieser Trend ist gekennzeichnet durch die Einführung fortgeschrittener Netzwerktechnologien wie PROFINET, CC-Link, EtherNet/IP und TSN für industrielle Anwendungen.
TSN Industrial erfüllt die Anforderungen der industriellen Automatisierung, wo präzise Synchronisation, Zuverlässigkeit und Determinismus entscheidend sind. TSN IA-Technologie hilft industriellen Netzwerken, ein hohes Maß an Synchronisation zu erreichen und rechtzeitige Datenlieferung zu gewährleisten. TSN ist die zugrunde liegende Technologie für Kommunikationsstandards wie PROFINET TSN, EtherNet/IP TSN, Sercos III TSN oder CC-Link IE TSN.
- PROFINET ist bekannt für seine Vielseitigkeit und Zuverlässigkeit. Seine Hochgeschwindigkeitsfunktionen und der Datenaustausch in Echtzeit sind in verschiedenen industriellen Umgebungen gut etabliert.
- CC-Link wurde entwickelt, um den Anforderungen von Hochleistungsanwendungen zu entsprechen. Dieses Protokoll unterstützt große Netzwerke und funktioniert mit verschiedenen Gerätetypen in kritischen Prozessen.
- EtherNet/IP, mit seiner offenen und interoperablen Architektur, integriert sich nahtlos in die bestehende IT-Infrastruktur, vereinfacht die Bereitstellung und Verwaltung und gewährleistet sichere Kommunikation zwischen Geräten verschiedener Hersteller.
3. Integration von Cloud und Analytik
Industrielle Cloud-Lösungen verändern die Industrie, indem sie den Schwerpunkt auf Analytik und vorausschauende Wartung legen, basierend auf einer robusten Serverinfrastruktur, unterstützt durch die notwendigen Sicherheitsmaßnahmen.
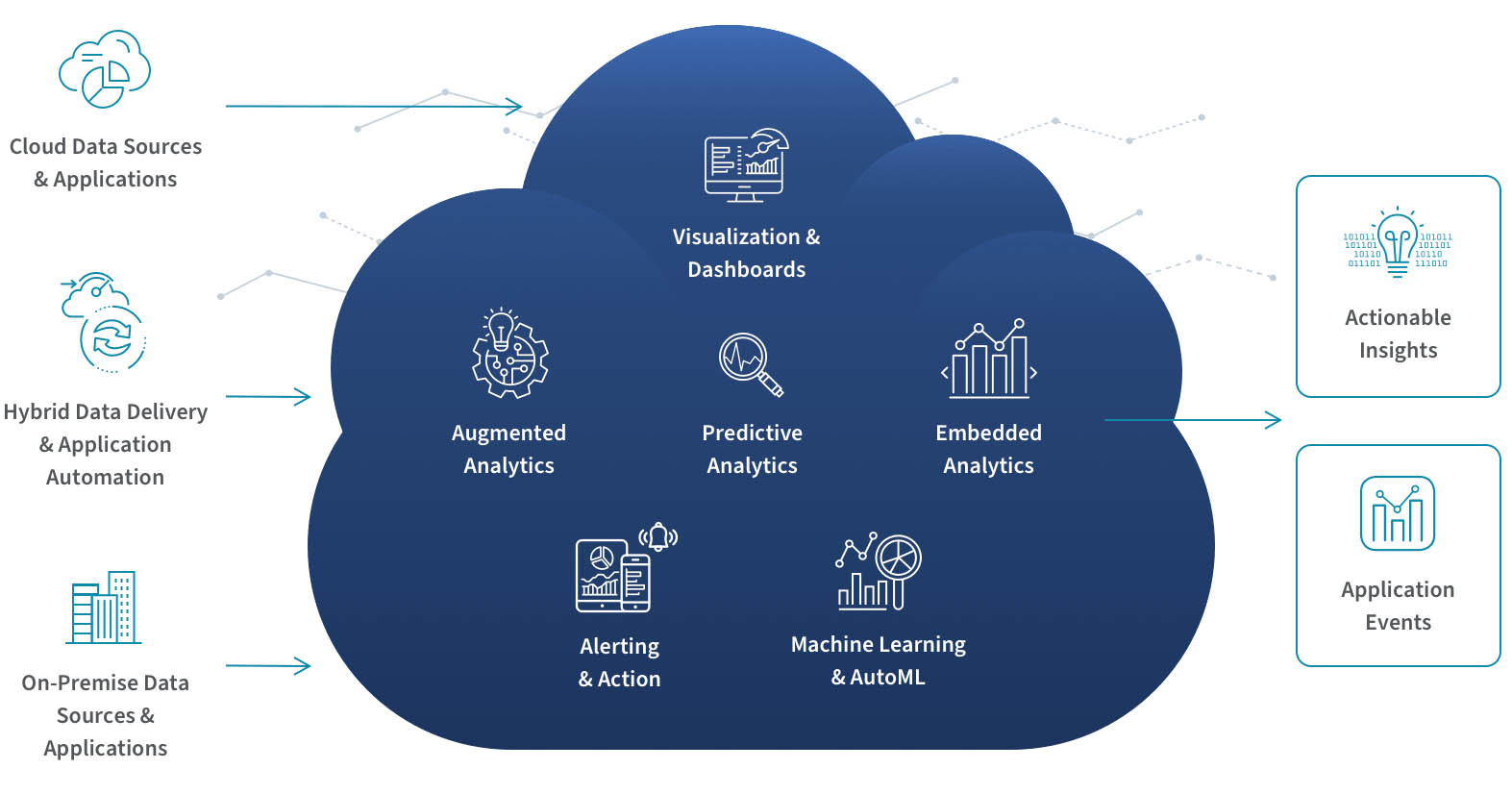
Cloud-basierte Datenanalytik und BI-Prozesse auf einer von Anbietern verwalteten Infrastruktur. Die Lösung von QlikTech als Beispiel
Das charakteristische Merkmal von Industrie 4.0 und Industrie 5.0 ist die Verbreitung von Geräten, die innerhalb des Cloud-Ökosystems für Echtzeitüberwachung, Analyse und Entscheidungsfindung vernetzt sind.
4. Erhöhte Systemsicherheit: SIL 3 Software-Konformität
Sicherheits-Integritätslevel 3 (SIL 3) ist durch die Norm IEC 61508 der Internationalen Elektrotechnischen Kommission definiert, um die Wirksamkeit eines Sicherheitssystems bei der Reduzierung gefährlicher Ereignisse zu messen.
In der Praxis bedeutet SIL 3 ein hohes Maß an Integrität des Sicherheitssystems. Die Software, die einem Sicherheitslebenszyklus durchläuft, wird überprüft und validiert und erreicht die SIL 3-Konformität durch unabhängige Bewertung durch zertifizierte Organisationen. Dieser Ansatz ist von entscheidender Bedeutung für Branchen, in denen die Folgen eines Fehlers zu schweren Personenschäden, großen Sachschäden oder Umweltschäden führen können.
Die steigenden Sicherheitsanforderungen manifestieren sich im Aufkommen von Software-Tools wie dem SIListra Safety Transformer und dem CODESYS Virtual Safe Control. SIListra fügt automatisch die codierte Verarbeitung in den Quellcode einer vollständigen Anwendung ein, die in C und C++ geschrieben wurde.
CODESYS Virtual Safe Control ist eine Softwarelösung, die einen Sicherheitscontroller simuliert. Sie überwacht und steuert Anlagen und gewährleistet den sicheren Betrieb gemäß definierten Standards ohne den Einsatz von physischen Sicherheitseinrichtungen. Sie testet und verifiziert die Sicherheitsfunktionen von Maschinen und Systemen in einer simulierten Umgebung.
5. Vorausschauende Wartung auf lokalen Servern
Vorausschauende Wartung und Edge-KI sind traditionell stark auf Hardware angewiesen. Fortschritte in der Softwaretechnologie haben sie jedoch zunehmend softwarezentriert gemacht. Algorithmen für vorausschauende Wartung werden auf lokalen Servern eingesetzt. Dieser Übergang ermöglicht eine bessere Integration mit Cloud-Systemen und bietet Zugang zu umfangreichen Rechenressourcen, was die Effizienz des vorausschauenden Wartungsprozesses erheblich verbessert.
Der neue Ansatz hilft Unternehmen, Kosten zu reduzieren, da der Bedarf physischer Hardware minimiert wird. Obwohl einige Aspekte der vorausschauenden Wartung möglicherweise immer noch Hardware erfordern, wird der Großteil des Prozesses – insbesondere Datenanalyse und operative Aufgaben – auf lokale Server an Industriestandorten verlagert, um sicherzustellen, dass die Wartung effizient in der Nähe der überwachten Anlagen und Prozesse durchgeführt werden kann.
6. Digitale Zwillinge
Das Konzept, einen digitalen Zwilling einer Fabrik zu erstellen, bei dem jeder Aspekt der physischen Umgebung in einem virtuellen Raum gespiegelt wird, bietet Unternehmen großartige Möglichkeiten zur Optimierung ihrer Abläufe. Von der Verfolgung von Palettenbewegungen bis zur Überwachung des Standorts von Personal und der Messung kritischer Parameter wie z.B. Spannungspegel kann ein digitaler Zwilling eine Vielzahl von Operationen nachbilden.
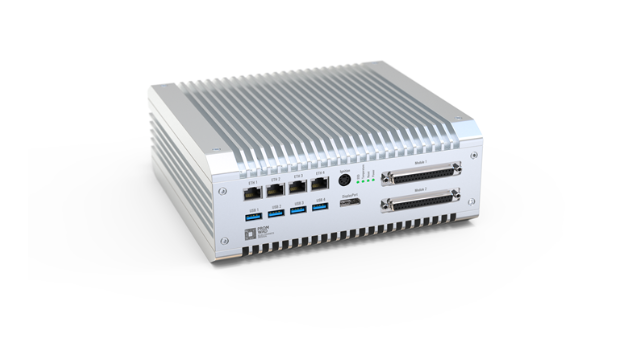
Ein von Promwad entwickelter digitaler Zwilling basierend auf Xilinx Kria SoM
Digitale Zwillinge ermöglichen auch eine vorausschauende Wartung zur schnellen Fehlerbehebung und Minimierung von Ausfallzeiten.
Lesen Sie unsere Fallstudie: Design digitaler Zwillinge für Regelkreise in industriellen Netzwerken.
7. Industrielles Metaverse als Game-Changer
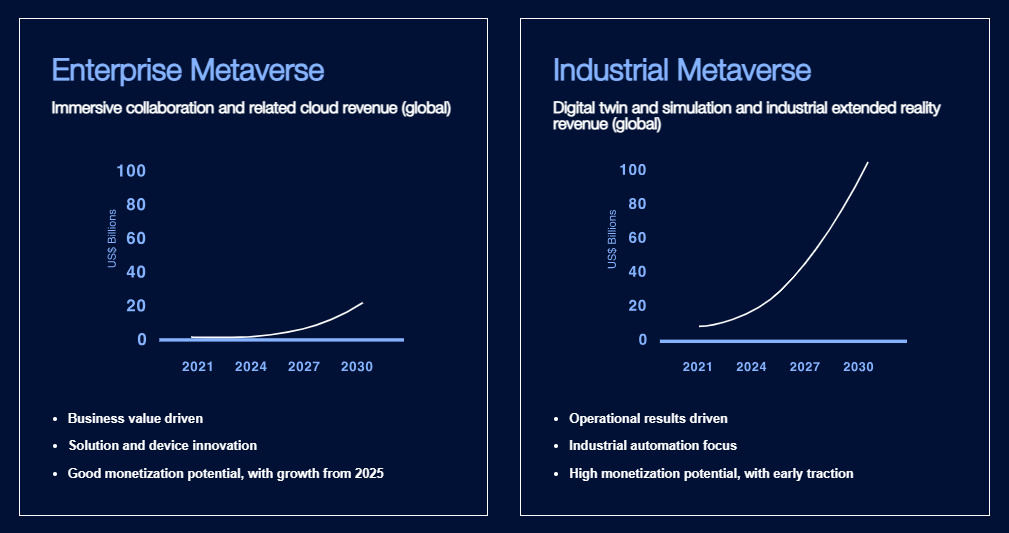
Unternehmens- und Industriemetaverse: Monetarisierungspotenzial in Milliarden US-Dollar ab 2025. Quelle: ABI Research, Bewertung der Unternehmensmetaverse-Chance, drittes Quartal, 2022
Dieses Metaverse hat das Potenzial, Arbeitsabläufe zu verändern und signifikante Vorteile für Unternehmen und die Gesellschaft zu bringen. Das industrielle Meta-Universum ermöglicht es Unternehmen, Design-Iterationen in einer physikbasierten Umgebung zu modellieren, zu prototypisieren und zu testen, so dass reale Probleme digital gelöst werden können.
Das industrielle Metaverse umfasst drei Schichten:
- Der digitale Zwilling ist der Hauptbestandteil des industriellen Metaversums. Physikalische Kopien sehen aus und verhalten sich wie virtuelle Repräsentationen von allem.
- Softwaredefinierte Automatisierung verbindet die reale und digitale Welt und beschreibt das Geschehen an Produktionsmaschinen. Heute sprechen SPSen industrielle Programmiersprachen; die nächste Generation sind virtuelle SPSen.
- Daten und KI. Im Metaverse werden rohe Zahlen mit Hilfe von Edge-Geräten und KI zu handlungsrelevanten Erkenntnissen. Edge-Geräte filtern die Daten und sammeln nur Wichtiges, und KI ermöglicht den Zugang auf das gesamte Wissen für besseres Engineering.
Schlüsselfähigkeiten und Ökosysteme für das Metaverse sind noch im Entstehen, einschließlich Konnektivität, Rechenleistung, Fidelität digitaler Zwillinge, Interoperabilität, Datenschutz und Sicherheit.
NVIDIA Omniverse ist eine der interessantesten Technologien, die zum industriellen Meta-Universum beitragen. Omniverse ist eine Plattform für Echtzeit-3D-Design-Zusammenarbeit und physikalisch genaue Modellierung. Sie ermöglicht es Ingenieuren, Designern und anderen Fachleuten, in gemeinsamen virtuellen Räumen zusammenzuarbeiten, um detaillierte Simulationen von realen Umgebungen und Prozessen zu erstellen. Sie kann Fabriken entwerfen, Arbeitsabläufe simulieren oder Modelle der künstlichen Intelligenz in einem virtuellen Raum trainieren, der die physische Welt widerspiegelt.
Die Trends der Industrieautomation im Jahr 2024 stehen für eine Bewegung hin zu mehr Konnektivität, Effizienz und Innovation. Während sich diese Trends weiterentwickeln, müssen Unternehmen dem Spiel immer einen Schritt voraus sein und die damit verbundenen Chancen nutzen.
Promwad hat sich verpflichtet, mit Unternehmen zusammenzuarbeiten, um die Kraft dieser Trends zu nutzen und die industrielle Automatisierung in die Zukunft zu führen. Unser Ingenieurteam ist bereit, mit Ihnen zusammenzuarbeiten und unsere Erfahrung und unser Wissen zu nutzen, um gemeinsam innovative Lösungen für Ihr Unternehmen zu entwickeln.
Lassen Sie uns gemeinsam die Zukunft gestalten! Wir sind bereit, Ihre Ideen auf dem Gebiet der industriellen Automatisierung zu diskutieren: