Hermetische Gehäuseabdichtung für elektronische Geräte. Teil 2: Polymer- und Metallschweißen
Wir befassen uns weiterhin mit Technologien zur Herstellung von versiegelten Gehäusen für Elektronik. Dieses Mal konzentrieren wir uns auf das Kleben und Schweißen, das zur Herstellung von Netzteilen, Kopfhörern, USB-Sticks und anderen nicht zerlegbare Geräten mit Schutz gegen Staub und Wasser verwendet wird.
Wir betrachten fünf Arten des Schweißens: Heizelementschweißen, Schweißen mittels elektromagnetischer Induktion, Vibration, Ultraschall und Laserschweißen. Und das wird nicht nur für Ingenieure und Technologen von Interesse sein. :-)
Im ersten Teil haben wir die Funktionsweise der gängigsten Abdichtungsmethoden anhand von Beispielen unserer Konstruktionen erläutert: Dichtungen und Gießen (Mehrkomponenten-Spritzgießen und Overmolding). Auch dieses Mal finden Sie eine Tabelle mit der Zusammenfassung aller Verfahren - um den Lesern dabei zu helfen, die beste Produktionstechnologie für ihr Hardwareprojekt auszuwählen.
Haftungsausschluss. In unserer Artikelserie geben wir unsere Erfahrungen in Elektronikdesign und -fertigung weiter. Wir verkaufen keine Geräte. Konkrete Beispiele von Schweißmaschinen werden nicht zu Werbezwecken gezeigt, sondern dienen lediglich der Veranschaulichung.
Natürlich eignet sich das Schweißen hervorragend für die Herstellung von dichten Metallgehäusen, aber wir werden uns auf Thermoplaste konzentrieren - spezielle Polymere, die beim Erhitzen schmelzen und dann wieder erstarren.
1. Heizelementschweißen: Wir verbinden das Gehäuse mit einer Teflonplatte
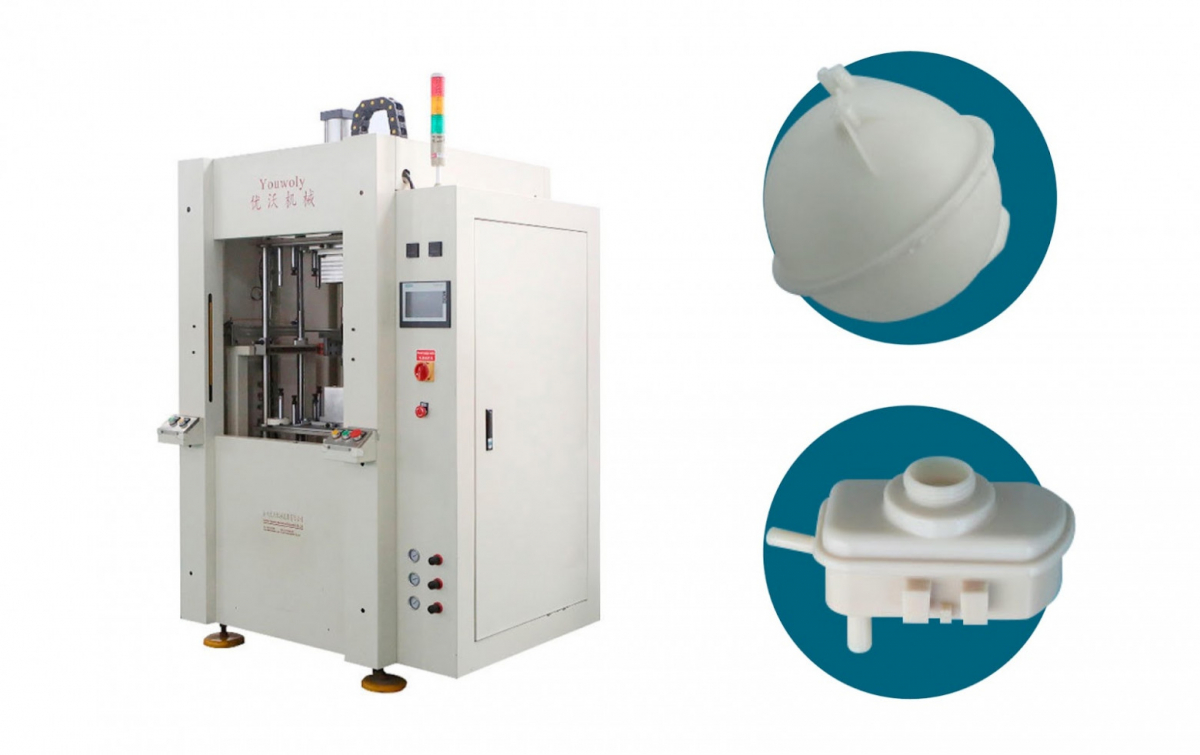
Heizelement-Schweißmaschine und Muster der hergestellten Produkte. Maschinenhersteller: Suzhou Youwoly Machinery Equipment Co., Ltd. (Shanghai, China). Bildquelle: made-in-china.com
Das Heizelementschweißen wird für die schnelle Montage von stabilen, dauerhaften und dichten Polymergehäusen für Elektronik verwendet.
Funktionsweise: Zwei geformte Gehäuseteile werden mit Hilfe einer Heizplatte zusammengefügt.
Das Prozessdiagramm ist unten abgebildet:
Arbeitsschritte beim Heizelement-Schweißen eines Kunststofferzeugnisses
- Zwei Gehäuseteile werden in einem bestimmten Abstand voneinander fixiert.
- Eine Heizplatte mit einer bestimmten Temperatur wird dazwischen gebracht. Die Gehäuseteile werden durch den Kontakt oder die unmittelbare Nähe zur Oberfläche der Heizplatte an der späteren Verbindungsstelle erwärmt. Die Haltevorrichtungen und die Strukturelemente, die die Komponenten in Position halten, bestimmen die anfängliche Schmelztiefe. Die Verweilzeit wird durch die Tiefe der sekundären Erweichung des Polymers festgelegt.
- Wenn die Verbindungsstellen die erforderliche Temperatur erreicht haben, öffnen sich die Haltevorrichtungen.
- Die Heizplatte wird entfernt
- Die Halterungen drücken die Gehäuseteile zusammen. Die Haltevorrichtungen bestimmen, wieviel Verbindungsmaterial beim Fügen verdrängt wird.
- In diesem Zustand werden die Gehäuseteile für kurze Zeit unter leichtem Druck gehalten, bis die geschmolzene Schicht abkühlt und eine Schweißnaht zwischen den beiden Verbindungsflächen entstanden ist.
Wenn die Kühlung abgeschlossen ist, gibt der Greifmechanismus einer der Halterungen das fertige Gehäuse frei.
Produktmuster, die mit dem Heizelement-Schweißverfahren hergestellt wurden. Die Muster wurden mit Maschinen von Suzhou Youwoly Machinery Equipment Co. hergestellt. (Shanghai, China). Bildquelle: made-in-china.com
Gehäuse werden häufig auf Teflon “gebacken”, da als Heizelement eine Aluminiumplatte mit einer dünnen Teflonschicht und einem Thermostatschalter verwendet wird. Diese Technologie sorgt für eine gleichmäßige Temperatur auf der gesamten Platte, während das Teflon verhindert, dass das geschmolzene Material an der Platte haften bleibt.
2. Elektromagnetisches Verschweißen des Gehäuses
Das elektromagnetische Schweißen ist ein einfaches, schnelles und zuverlässiges Verfahren für die Montage von Struktur- und Druckdichtungen. Es ist für die meisten thermoplastischen Materialien geeignet und wird oft bei Hochdruckdichtungen eingesetzt. Diese Verfahren ermöglicht das Verschweißen von heterogenen Thermoplasten, Papier und Aluminium mit Thermoplasten (verstärkt und unverstärkt).
Das Prozessdiagramm ist unten abgebildet:
Funktionsweise:
- Das Schweißgerät verfügt über eine Induktionsspule, die mit Hochfrequenzstrom betrieben wird.
- Das hochfrequente elektromagnetische Feld wirkt auf einen eingebetteten elektrisch leitfähigen oder ferromagnetischen Schweißzusatz ein, erhöht dessen Temperatur und bringt ihn zum Schmelzen.
- Der geschmolzene Schweißzusatz schweißt die Gehäuseteile durch eine thermoplastische, elektromagnetische Verbindung zusammen.
Der eingebettete Schweißzusatz für dieses Schweißverfahren besteht aus einer Dispersion von mikroskopisch kleinen Metallpulvern - Eisen, Edelstahl, Graphit oder Ferrit - und wird durch das elektromagnetische Feld erhitzt.
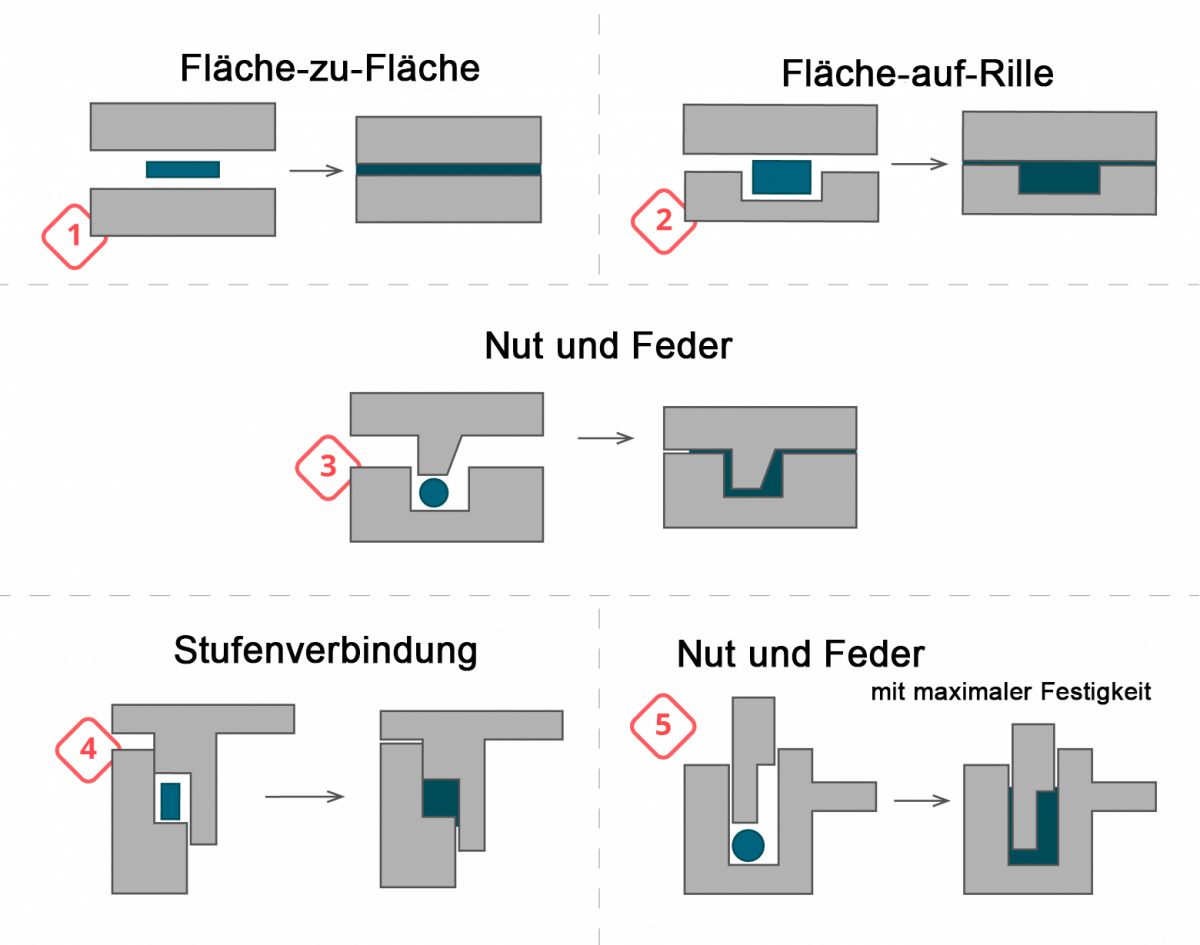
Verbindungsarten von thermoplastischen Teilen beim Induktionsschweißen
- Fläche-zu-Fläche ist gut geeignet für lange Schweißnähte. Wird in Sollarzellen verwendet.
- Fläche-auf-Rille wird in Armaturenbrettern von Autos verwendet.
- Die Nut- und Federverbindung ist eine sehr starke Verbindung, die Methode ist gut geeignet für extreme Belastungen und enge Verbindungen.
- Stufenverbindungen werden zum Verbinden von Kunststoffteilen verwendet, die Vibrationsbelastungen standhalten müssen.
- Die Nut- und Federverbindung mit maximaler Kraft wird für Hochdruckdichtungen verwendet.
Gehen wir näher auf die Vor- und Nachteile dieser Methode ein:
Vorteile des elektromagnetischen Schweißens:
- Für alle thermoplastischen Materialien geeignet, sowohl kristalline als auch amorphe
- Die Dicke des Produkts bleibt erhalten, und die Schweißnähte können verdeckt werden, da das Schmelzen von innen erfolgt
- Minimaler Anpressdruck und schnelle Schweißzyklen
- Kann für hohe Produktionsmengen automatisiert werden
- Einfache Realisierung von strukturellen, hermetischen und Hochdruck-Dichtungen
- Die physikalischen und chemischen Eigenschaften des geschweißten Bereichs entsprechen denen der zu verbindenden Materialien
- Geschweißter Bereich kann beliebig groß sein: von einem kleinen Punkt bis zu 3 m
- Hohe Haltbarkeit des elektromagnetischen Verbindungsmaterials
- Saubere und leise Montage
Nachteile des elektromagnetischen Schweißens:
- Nicht geeignet für das Schweißen elektrischer Geräte, die mit Thermoplasten ummantelt sind: Wicklungsspulen, Magnete, Leiterplatten, Sensoren, usw.
- Erfordert das Schweißen von Prototypen für die Montage neuer Produkte, da die elektromagnetische Schweißung von der Schweißspule und der Fähigkeit abhängt, die komplexe Oberflächen der Fügeteile zu berechnen
- Hohe Kosten für Schweißgeräte
- Elektromagnetische Schweißspulen neigen zu Überlastung und Überhitzung
3. Vibrationsschweißen
Das Vibrationsschweißen zum Verbinden thermoplastischer Kunststoffe beruht auf dem Prinzip des Reibschweißens: Die Wärme zum Aufschmelzen des Thermoplasts wird erzeugt, indem ein Teil gegen ein anderes gepresst und durch eine kleine relative Verschiebung in der Fügeebene in Schwingung versetzt wird. Durch die Hitze schmilzt der Thermoplast an der Grenzfläche. Wenn die Vibration aufhört, richten sich die Teile automatisch aus.
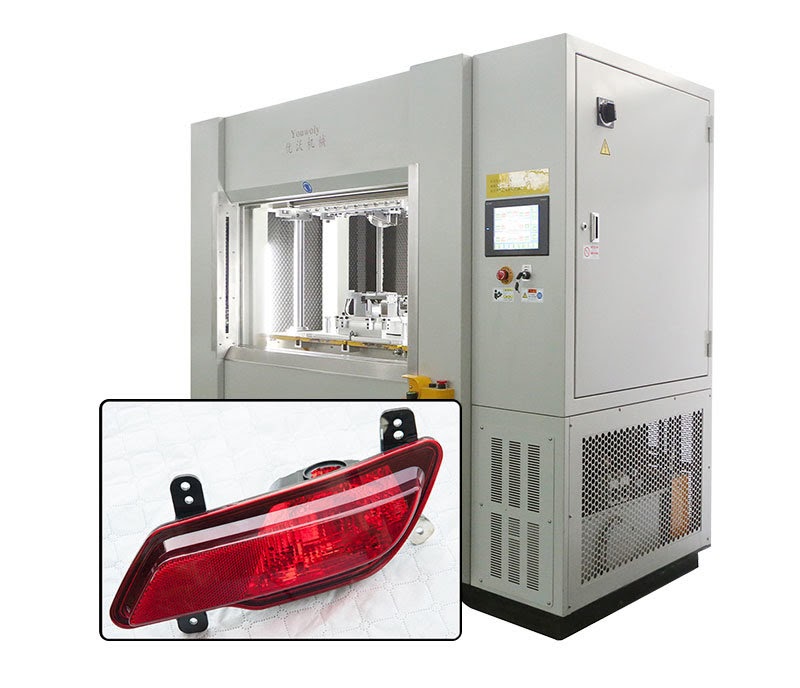
Vibrationsschweißmaschine und Produktmuster. Hersteller: Suzhou Youwoly Machinery Equipment Co. (Shanghai, China). Bildquelle: made-in-china.com
Die Schmelzzeit des Materials beträgt beim Vibrationsschweißen in der Regel 2-3 Sekunden. Die Gesamtzykluszeit beträgt im Durchschnitt 6 bis 15 Sekunden, einschließlich Be- und Entladen.
Das Vibrationsschweißen ist in der Automobilindustrie für die Herstellung von Teilen weit verbreitet.
4. Ultraschallschweißen
Ultraschallschweißen ist ein schnelles, sauberes und effizientes Verfahren zum Zusammenfügen von starren thermoplastischen Spritzgussteilen. Es wird in allen Industriezweigen verwendet, um zwei Kunststoffe oder Kunststoffe mit Nicht-Kunststoffen zu verbinden.
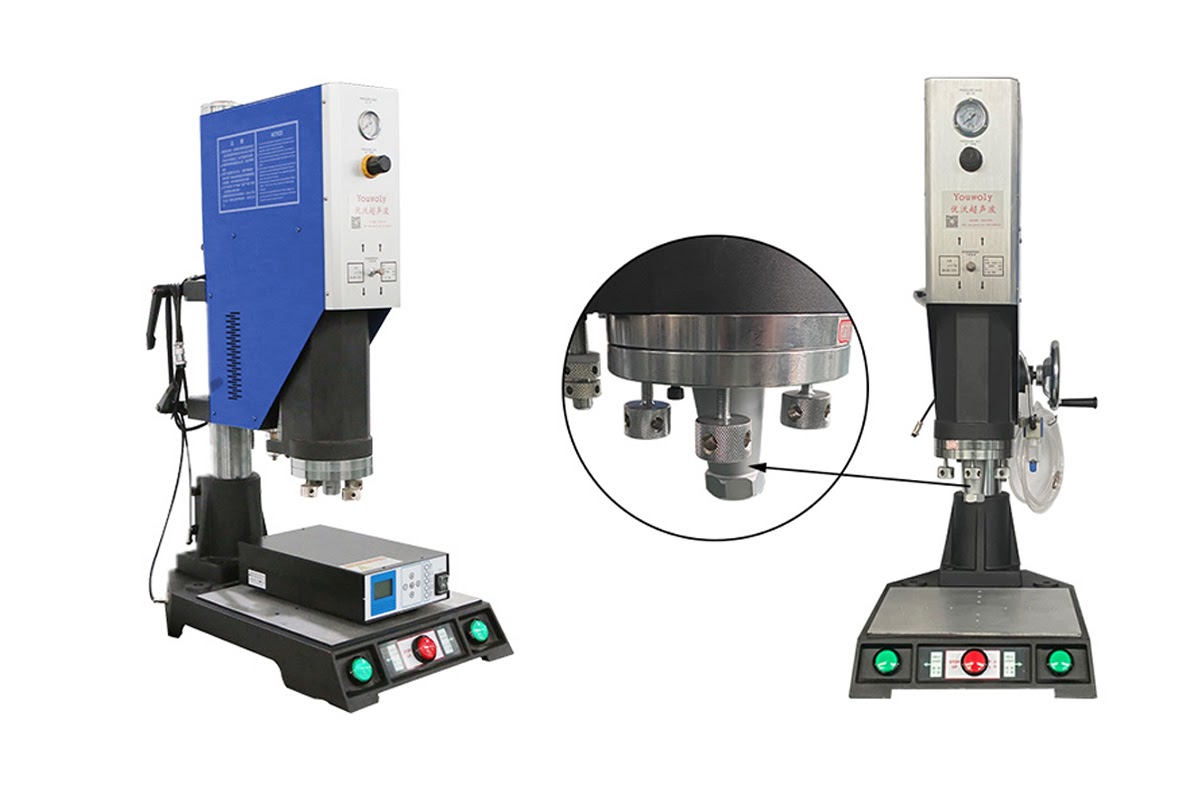
Ultraschall-Schweißmaschine. Hersteller: Suzhou Youwoly Machinery Equipment Co. (Shanghai, China). Bildquelle: made-in-china.com
Ultraschall- oder Vibrationsschweißen erlauben eine wirtschaftlichere Produktion der Teile. Beim Ultraschallschweißen wird das fertige Produkt in 0,1 bis 3 Sekunden hergestellt, und auch die Maschinen sind kostengünstiger. Die Maschine auf dem Foto oben kann zum Beispiel für 2.000 bis 3.000 $ erworben werden, während die Preise für andere in diesem Artikel gezeigte Geräte bei 15.000 bis 18.000 $ beginnen. Mittels Vibrationsschweißen können jedoch auch größere und komplexere Teile geschweißt werden.
Typische Beispiele für Geräte, die mittels Ultraschallschweißen hergestellt werden
Das Ultraschallschweißen ist eine hervorragende Alternative zu Klebstoffen, Lösungsmitteln und mechanischen Befestigungen für die Herstellung von dichten, nicht zerlegbaren Gehäusen, z.B. für Netzteile, Kopfhörer oder Ladegeräte.
Vorteile des Ultraschallschweißens:
- Energieeffizienz und hohe Produktivität bei geringeren Kosten als bei vielen anderen Montageverfahren
- Erfordert keine komplexen Belüftungssysteme, um Rauch oder Wärme abzuleiten
- Einfach in eine automatisierte Montagelinie zu integrieren
- Sofortiger Start und Stopp ohne Restwärme
5. Laserschweißen
Die Laserschweißtechnik ähnelt dem IR-Schweißen, sie ist ebenfalls berührungslos. Die benötigte Wärmeenergie wird durch den Laserstrahl, der auf die Oberflächen der zu schweißenden Teile fokussiert wird, in das Werkstückmaterial eingebracht.
Funktionsprinzip des Laserschweißens
In manchen Fällen kann sich die Mitte der Fügezone stärker erwärmen als die Randbereiche - so bewirkt der Schweißvorgang eine intensive Durchmischung der Schmelze im Fügebereich, was zu einer extremen Festigkeit der Schweißnaht beiträgt. Die thermische Ausdehnung der Schmelze sorgt für die erforderliche Schweißkraft, um die vorfixierten Teile zu verbinden.
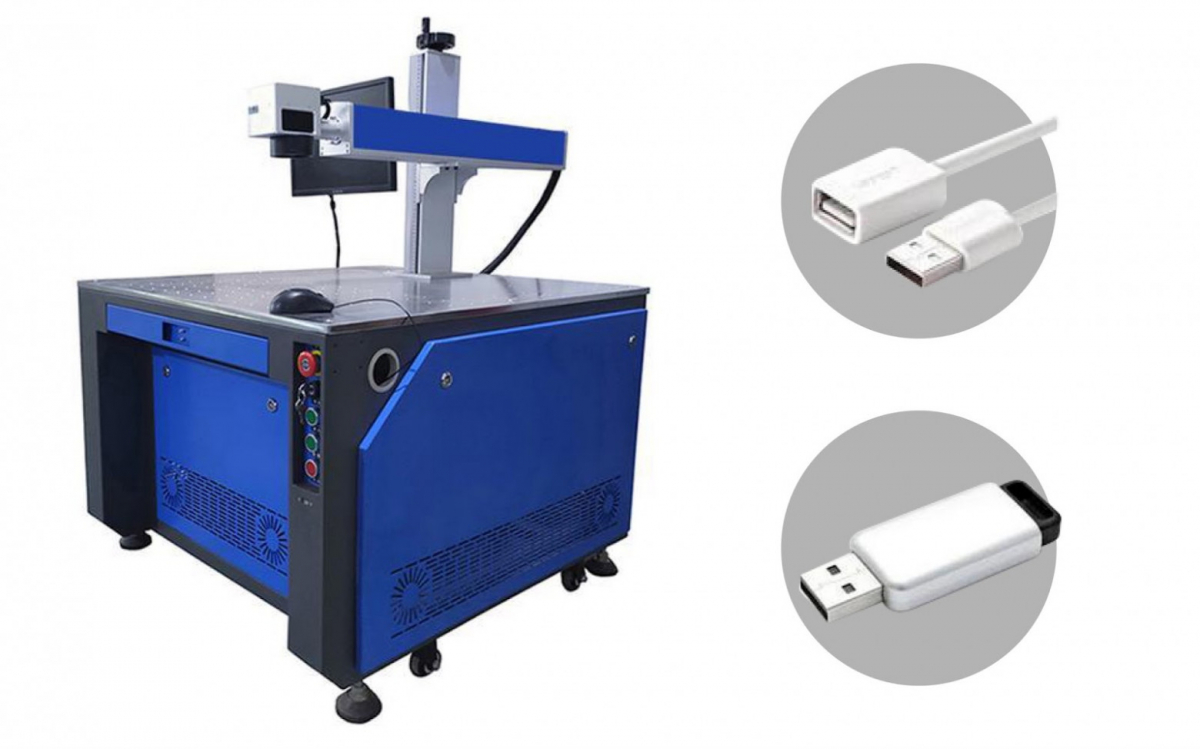
Laserschweißmaschine Intouch und Produktmuster. Maschinenhersteller: Taiyi Laser Technology Company Ltd. (Shenzhen, China). Bildquelle: made-in-china.com
Das Laserschweißen ist ein beliebtes Verfahren zum Abdichten von Steckverbindern in der Elektronik.
6. Klebeverfahren
Das Kleben ist eine der praktischsten Methoden zum Zusammenfügen eines thermoplastischen Produkts mit ähnlichen oder anderen Materialien, einschließlich Metallen. Der Klebstoff verteilt die Belastung über die gesamte Klebeoberfläche und kann bei Bedarf für Dichtheit sorgen.
Flexible Klebstoffe lassen eine gewisse Bewegung zwischen den zu verklebenden Oberflächen zu und können so Unterschiede in den linearen Wärmeausdehnungskoeffizienten der Materialien ausgleichen. Außerdem sind Klebstoffe relativ kostengünstig und erfordern keine teure Spezialausrüstung.
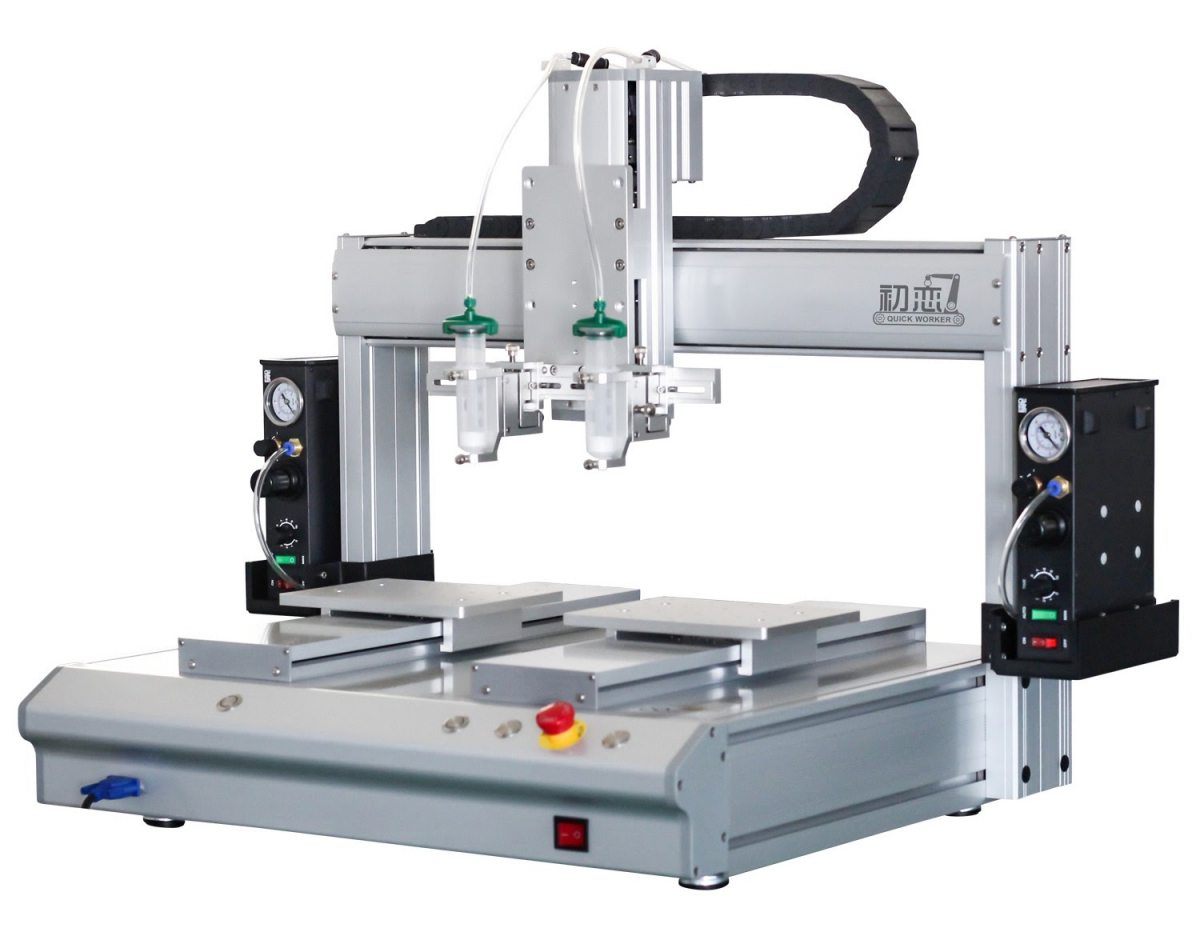
Automatischer Klebstoffspender mit Positionierungssystem. Gerätehersteller: First love robot Co. (Dongguan, China). Bildquelle: made-in-china.com
Vorteile des Klebens bei der Herstellung von Gehäusen:
- Niedrige Gerätekosten. Einfache Bedienung bei automatischen Geräten
- Heterogene Materialien können miteinander verbunden werden
- Elastizität und Dichtheit
- Geringe Kosten und einfache Reparatur
Schlussfolgerungen
Wie Sie bereits aus dem ersten Teil des Artikels über Gießverfahren und Dichtungen wissen, beeinflussen mehrere Faktoren die Wahl der idealen Methode zum Abdichten eines Gehäuses für ein bestimmtes Gerät: Konstruktionsanforderungen, Produktionskapazität, Losgröße, Budget, Betriebsbedingungen u.a.
Hier finden Sie eine zusammenfassende Tabelle mit einer Übersicht über alle Technologien, die wir in beiden Teilen behandelt haben:
Gießverfahren und Dichtungen aus Teil 1
Methode der Versiegelung | Maschine | Vorteile | Nachteile |
Mehrkomponenten-Spritzgießen | Spritzgießmaschine mit zwei Spritzeinheiten und teurer Ausrüstung | Geringe Kosten in der Massenproduktion, keine zusätzlichen Kosten für die Versiegelung | Nicht erschwinglich bei kleinen Serien. Erfordert teure Maschine, Ausrüstung und hochqualifiziertes Personal |
Overmolding | Spritzgießmaschine und verschiedene Ausrüstungssätze | Die Alternative zum Mehrkomponentenguss. Aufgrund der einfacheren Ausrüstung ist die Technologie für kleine Stückzahlen kostengünstiger. | Kosten für Bediener oder manuelle Arbeit |
Verwendung einer Dichtung | Nicht erforderlich | Geringe Kosten, keine Maschine erforderlich | Zusätzlicher Montageschritt (Dichtungseinbau), Befestigung im Dichtungsbereich erforderlich |
Methode der Versiegelung | Maschine | Vorteile | Nachteile |
Heizelementschweißen | Heizplatte mit dünner Teflonschicht, Klammern | Einfaches Verfahren, robuste Verbindung für fast alle Thermoplaste | Zusätzliche Bearbeitung der Schweißnähte, langer Zykluszeit, benötigt ebene Flächen |
Elektromagnetisches Schweißen | Induktive Schweißer | Fügen von unterschiedlichen Materialien. Die Nähte sind unsichtbar. Schweißen entlang komplexer Profile möglich. Kurze Zykluszeiten. Kann automatisiert werden. Hochdruckdichtungen einfach zu realisieren | Teure Ausrüstung, Prototyping-Verfahren erforderlich. Nicht geeignet für das Schweißen von thermoplastisch ummantelten elektrischen Geräten (Wicklungsspulen, Magnete, Leiterplatten, Sensoren) |
Vibrationsschweißen | Anlage zum Vibrationsschweißen | Kurze Zykluszeiten | Flache Schweißfläche. Gefahr der Beschädigung von elektronischen Bauteilen durch Vibration. Nur für kompatible Thermoplaste geeignet. Gefahr der Verschiebung der Teile |
Ultraschallschweißen | Ultraschall-Schweißmaschinen, tragbare Geräte und Handpistolen | Kurze Zykluszeiten, hohe Energieeffizienz und Produktivität. Arbeitet im automatischen Montagezyklus. Unauffällige Schweißnähte. Umweltfreundlich. Geeignet zum Verbinden unterschiedlicher Materialien | Nicht geeignet zum Verbinden dickwandiger Bauteilen. Feuchtigkeitsempfindlich |
Laserschweißen | Laserschweiß-Anlage | Kurze Zykluszeiten, gutes Aussehen. Minimale Temperaturtoleranz. Umweltfreundlich. Verbinden unterschiedlicher Materialien möglich | Teure Ausrüstung |
Kleben | Halterungen | Einfach, kostengünstig. Gleichmäßige Spannungsverteilung: Ungleiche Materialien können verbunden werden, auch solche, die beim Schweißen brechen | Vorbereitung der Oberflächen erforderlich, lange Aushärtungszeit. Toxizität. Geringere Festigkeit im Vergleich zu geschweißten Verbindungen |
Wir hoffen, dass Sie von unseren Erfahrungen in der Konstruktion und Herstellung von geschlossenen Gehäusen profitieren können.
Unsere Projekte