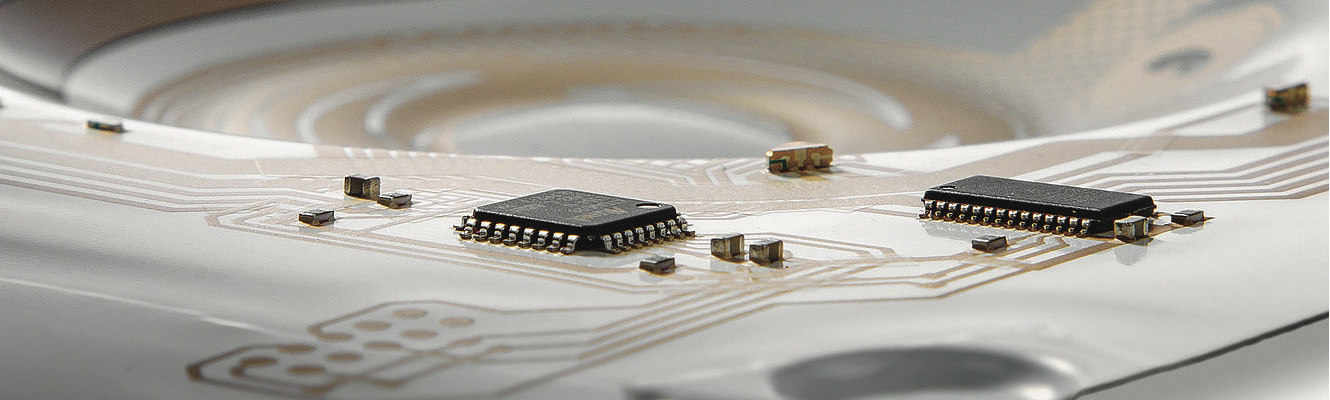
In-Mold Electronics (IME): wie es funktioniert und warum es ein neuer Trend ist
Seit einigen Jahren diskutieren Elektronikhersteller über eine bahnbrechende Technologie, die unsere Geräte und die Herangehensweise an ihr Design verändern wird: keine mechanischen Tasten und Schalter mehr, Reduzierung der Dicke auf 2 mm, ca. 70 % leichter und 30 % billiger. Wir sprechen hier nicht über zukünftige Massengeräte wie den doppelt faltbaren Bildschirm, den Samsung kürzlich vorgestellt hat, sondern über ein Produktionsverfahren, das bereits in der Industrie- und Automobilelektronik, bei Haushaltsgeräten und IoT-Gadgets eingesetzt wird. Diese Technologie wird „Molding mit integrierter Elektronik“ oder In-Mold Electronics (IME) genannt. Leider haben wir in unserem Blog noch nicht über dieses spannende Thema berichtet. Das wollen wir nun nachholen.
Wir wollen gleich im Voraus verraten, dass IME keine grundsätzlich neue Technologie ist, sondern eine Weiterentwicklung von Verfahren, die schon früher eingesetzt wurden. Mit dem Aufkommen dehnbarerer Materialien und besser leitfähiger Tinten, die dem Guss bei hohen Temperaturen standhalten, konnte man auf starre Leiterplatten verzichten und Leiterbahnen direkt auf Kunststoffoberflächen von elektronischen Geräten aufbringen.
Automobilkonsolen, die mit IMSE-Technologie entwickelt und hergestellt wurden. Quelle: Tactotek
Dadurch war es möglich, von der starren 2D-Elektronik wegzukommen und zu flexiblen Folienplatinen und 3D-Strukturelektronik mit Widerständen, integrierten Schaltkreisen, Sensoren, Antennen und LEDs zu wechseln, die die gekrümmten Formen der Gehäuse verschiedenster Geräte annehmen können.
Bestandteile einer integrierten Elektronik können sein:
- Elektrische Schaltungen: flexible Leiterplatten und Verdrahtung
- Beleuchtung: ein- oder mehrfarbige Indikatoren, animierte Beleuchtungen und Logos
- Bedienelemente: aufgedruckte kapazitive Touch-Bedienelemente, gegossene Kunststoffoberflächen für 2D- und 3D-Bedienelemente
- Sensoren: Umgebungslicht-, Stoß-, Stress-, Näherungs- und Beschleunigungssensoren
- Antennen: NFC, Bluetooth/WLAN
- Integrierte Schaltungen: MCU, BL
Sehen wir uns nun alles der Reihe nach an. Das Molding mit integrierter Elektronik ist eine Art der In-Mold Decoration (IMD), über die wir bereits gesprochen haben. Bei IMD werden Gehäuse für elektronische Geräte unter Druck direkt in Formen oder im Prozess des Blasformens dekoriert.
Das Ergebnis ist ein fertiges Teil, das keine zusätzliche Oberflächenbehandlung, Markierung oder Lackierung benötigt.

Das Prinzip des In-Mold Labeling (IML). Quelle: Maspi S.r.l.
Das Bild oben zeigt das grundlegende Verfahren der IMD- und IML-Technologien:
- Zunächst wird das gewünschte Muster - Text, Dekor oder Textur (z. B. ein Firmenlogo oder Tastenbeschriftungen) - auf einen dünnen Kunststofffilm aufgebracht. Dies geschieht im Sieb- oder Digitaldruck. Als Ergebnis erhält man sogenannte „In-Mold-Applikationen“ oder Etiketten
- Die Applikation wird zum Gießen in eine Form gelegt.
- Dann wird trockenes Polymergranulat in die Formmaschine gegeben, geschmolzen und mit Druck in die Form gepresst - hinter oder vor der Folie.
- Das bedruckte Etikett verschmilzt mit dem Kunststoff und nimmt beim Aushärten die Form der Gussform an.
- Am Ende des Prozesses, wenn die Form geöffnet wird, erhält man das fertige Gehäuseteil aus Kunststoff mit integrierter Grafik.
In-Mold Decoration macht es möglich, die Ideen der Industriedesigner auch bei strukturell komplexen Kunststoffteilen zu verwirklichen. Darüber hinaus sind die mit IMD gestalteten Elektronikgehäuse langlebig und kratzfest.

Eine mit IMD entworfene Fernbedienung
Das Foto oben zeigt die Oberseite einer Fernbedienung, die mit In-Mold Decoration (IMD) entworfen wurde. Weitere bekannte Beispiele für Geräte, die mit dieser Technologie hergestellt werden, sind Multimeter, Armaturenbretter von Fahrzeugen, Spielzeug und Mobiltelefone.
Was ist der Unterschied zwischen In-Mold Decoration (IMD) und In-Mold Labeling (IML)?
Wird eine Grafik oder Textur innerhalb der Form nicht auf der gesamten Oberfläche des Gehäuses- von Kante zu Kante - sondern nur auf einem separaten Bereich aufgebracht, nennt man diese Art der Dekoration In-Mould Labeling (IML). Mit dieser Technologie können Farbe, grafische Elemente und texturierte Bereiche hinzugefügt werden.
IML wird häufig verwendet, um Logos, Warnzeichen, Zertifikatssymbole, Teilenummern oder kurze Anweisungen hinzuzufügen. Man findet diese Etiketten häufig auf Einwegverpackungen und Kunststoffbehältern für den Hausgebrauch.
Und jetzt kommen wir zurück zur In-Mold Elektronik, die eine logische Fortsetzung der beiden vorherigen Technologien darstellt. Es scheint, dass die erste kommerzielle Anwendung von IME in einer innovativen Overhead-Konsole für ein Ford-Fahrzeug im Jahr 2012 stattfand. Heute wird IME für Haushaltsgeräte, Armaturenbretter von Fahrzeugen, medizinische Geräte, in der Luft- und Raumfahrt und bei Wearables eingesetzt.
Diese Technologie kombiniert die dekorative Anwendung des IMD-Verfahrens mit voll funktionsfähiger Elektronik. Allerdings wird die Folie in diesem Fall nicht mit Dekor oder Text bedruckt, sondern mit Leiterbahnen aus leitfähigen Silberfarben. Und auch Widerstände, Mikroschaltungen und LEDs könne auf die Folie aufgebracht werden.
Durch das Spritzgussverfahren entstehen dünnwandige (bis zu 2 mm) Kunststoffteile mit ausreichender Festigkeit, hoher Funktionalität und zusätzlicher Beleuchtung, Tastaturen und Dekorelementen.
Das Bild unten zeigt, wie dies funktioniert:
Bildquelle: Functional Ink Systems Presentation for „In-Mold Electronics“ by DuPont
-
Siebdruck von Grafiken und Leiterbahnen mit Funktionstinten auf dünne Polyester- oder Polycarbonatfolien
-
Durch das Thermoformen erhalten die bedruckten Medien eine dreidimensionale Form, die der Spritzgussform entspricht
-
Spritzgießen
IME-Produkte sind in der Regel thermogeformt, aber nicht immer. In Bereichen mit einer Touchscreen-Oberfläche kann die Oberfläche zum Beispiel flach bleiben.
Ein aufkommender Trend ist die Verwendung von Polyethylenterephthalat (PET), das sich zwar nicht gut formen lässt, aber für Designs mit einem kleineren Krümmungsradius geeignet ist. Allerdings verträgt PET keine große Hitze, so dass der Elektronikmarkt jetzt Niedertemperatur-Lote benötigt.
Während der Verbraucher diese Technologie noch als innovativ wahrnimmt, wirken die Leiterbahnen selbst wie dekorative Elemente :-) Mit der Zeit werden Industriedesigner und Hardware-Startups sicherlich mit Ideen aufwarten, wie man die Möglichkeiten dieser neuen Gussart ausnutzen kann.

Bildquelle: Analysebericht von IDTechEx 2020
Das Foto oben zeigt Seriengeräte und Prototypen, die mit In-Mold-Elektronik hergestellt wurden. Beispiel für IME-Produkte findet man häufig auch in neuen Fahrzeugen und Haushaltsgeräten, bei denen sich die Form der Elektronik vollständig an die gekrümmten Oberflächen des Designs anpasst.
Diese Designs verfügen nicht mehr über die traditionellen Knöpfe, Sensoren und andere Funktionsschalter. An ihre Stelle sind visuelle Touchscreen-Oberflächen getreten. Mit IME können Beleuchtungen, Anschlüsse, Mikroschaltungen, Sensoren oder kapazitive Touchpads in nahezu jedes gebogene Teil integriert werden.
Die geformten IME-Geräte und die eingebettete Elektronik sehen nicht nur schön aus, sie sind auch funktional und zuverlässig. Durch die Reduzierung von mehreren Teilen und beweglichen Komponenten werden sowohl das Risiko von Ausfällen, als auch die Herstellungs-, Montage- und Wartungskosten reduziert.
Kapazitive Touch-Steuerung und Benutzeroberflächen
Kapazitive Touch-Steuerung wird in vielen IME-Anwendungen eingesetzt. Diese Schnittstelle ersetzt das Drücken einer physischen Taste durch die Berührung mit einem Finger. Die Leiterbahnen auf der Platine befinden sich unterhalb des Berührungspunktes und überwachen die Veränderung des elektrostatischen Feldes. Bei Berührung der kapazitiven Platte wird eine kleine Ladung zum Berührungspunkt gezogen – unser Finger wirkt als funktionaler Kondensator. In Fahrzeugen werden solche Schnittstellen zum Beispiel zum Einschalten der Scheinwerfer, der Stromversorgung oder zum Einstellen der Lautstärke verwendet.
So präsentiert das US-Chemieunternehmen Dupont, einer der weltweit führenden Entwickler von leitfähigen Tinten für IMEs, Schnittstellen für Autos der Gegenwart und Zukunft:


Bildquelle: Functional Ink Systems Presentation for „In-Mold Electronics“ by DuPont
Abschließende Betrachtung
Die Automobilindustrie ist nur eine der vielen Anwendungen von IME, die wir oben bereits erwähnt haben. Schauen wir uns ein Fallbeispiel aus diesem Bereich an, um das Thema dieses Artikels zu veranschaulichen. Nehmen wir die Overhead-Konsole in einem Auto, die mit einer Leiterplatte und einem klassischen Kunststoffgehäuse mit einer Vielzahl von Komponenten und vorgefertigten Teilen konstruiert wurde, und vergleichen sie mit einer Konsole des finnischen Unternehmens TactoTek, das jetzt seine IMSE (In-Mold Structural Electronics) genannte Technologie entwickelt:

Bildquelle: Functional Ink Systems Presentation for „In Mold Electronics” by DuPont
Standardentwicklung | IME-Entwicklung | Unterschied | |
---|---|---|---|
Gewicht | 650 g | 150 g | −77% |
Dicke | 45 mm | 3 mm (flat version) | −93% |
Mechanische Teile; | 64 pcs. | 2 pcs. | −96% |
PCBA-Größe | 10 x 4 sm | 10 x 3 sm | −25% |
Vergleich zwischen herkömmlichem und IME-basierten Design einer Konsole
Wie ma sieht, kommt es zu einer deutlichen Reduzierung des Gewichts, der Größe, der Anzahl der beweglichen Teile und damit zu einer Erhöhung der Zuverlässigkeit und der Kosten des Gerätes insgesamt. Glaubt man Analystenberichten zur Entwicklung dieser Technologie, die eine Zunahme der IME-Implementierungen ab 2023-2024 vorhersagen, zeichnet sich ein neuer Trend auf dem Elektronikmarkt ab - der Übergang von flachen und starren Leiterplatten in einem kastenförmigen Gehäuse zu dreidimensional strukturierter Elektronik.
Wenn Ihre Arbeit also mit Hardware-Design und Elektronikprodukten zu tun hat, sollten Sie sich diesen Trend genauer ansehen, um nicht den Anschluss zu verpassen. Was das Promwad-Ingenieurteam betrifft, so hoffen wir, dass wir bald in der Lage sein werden, in einer eigenen Fallstudie über das Design und die Produktionseinführung von In-Mold Electronics berichten zu können.
Unsere Projekte